OEE-Institute® Mehr Output. Weniger Stillstand. Höhere Gesamtanlageneffektivität.
Willkommen beim OEE Institute® – Ihrem Partner für echte Produktionsoptimierung. Ich bin Heinz-Joachim Schulte, Gründer und CEO. Mit über 40 Jahren Erfahrung in der produzierenden Industrie helfe ich Unternehmen, ihre Gesamtanlageneffektivität (OEE) messbar zu verbessern. Direkt. Klar. Ohne Umschweife.
Warum das wichtig ist?
Weil jede Minute Stillstand Geld kostet. Und weil Maschinenstillstände, lange Rüstzeiten und unklare Prozesse keine Schicksale sind – sondern lösbare Probleme. Ich zeige Ihnen, wie Sie Kosten senken, Verluste minimieren und gleichzeitig den Rohertrag steigern.
Für wen ist das hier?
Für Produktionsleiter, Instandhaltungsverantwortliche, Geschäftsführer, Werksleiter und Investoren, die mehr aus ihren automatisierten Produktionslinien herausholen wollen. Sie wollen Fakten statt PowerPoint? Dann sind Sie hier richtig.
Was dürfen Sie erwarten?
- Eine klare Analyse Ihrer Produktionsprozesse
- Praktische Lösungen zur Effizienzsteigerung
- Konkrete Maßnahmen zur OEE-Verbesserung
- Keine Theorie – nur echte Industrieerfahrung
Heinz-Joachim Schulte
Gründer und CEO
Was ist OEE?
Die Gesamtanlageneffektivität (kurz: OEE) ist eine Kennzahl, die die Effizienz einer Produktionsanlage misst. Sie gibt an, wie gut die Anlage genutzt wird, um Produkte herzustellen. Die OEE setzt sich aus drei Faktoren zusammen:
1. Verfügbarkeit:
Wie viel Zeit ist die Anlage einsatzbereit? Hier werden beispielsweise Ausfallzeiten aufgrund von Reparaturen oder Wartungsarbeiten berücksichtigt.
2. Leistung:
Wie schnell arbeitet die Anlage? Hier wird die tatsächliche Produktionsrate mit der maximal möglichen Produktionsrate verglichen.
3. Qualität:
Wie hoch ist die Qualität der produzierten Produkte? Hier wird berücksichtigt, wie viele fehlerhafte Produkte hergestellt werden.
Die Gesamtanlageneffektivität gibt also an, wie gut eine Produktionsanlage genutzt wird, indem sie die Auswirkungen von Ausfallzeiten, Geschwindigkeit und Qualität auf die Produktionsleistung berücksichtigt.
OEE-Institute informiert:
"Made in Germany" oder "Arbeitsplätze über den Zaun werfen"
Interview:
Warum Produktionsoptimierung mit OEE
so wichtig ist.
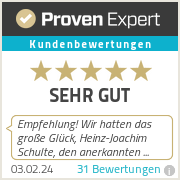
Warum sollten Sie OEE in Ihrem Produktionsbetrieb einsetzen?
Es gibt mehrere Gründe, warum die Verwendung der Gesamtanlageneffektivität (OEE) in Ihrem Produktionsbetrieb sinnvoll sein kann:
- Verbesserung der Effizienz:
Die OEE zeigt Ihnen auf einen Blick, wie effizient Ihre Anlage genutzt wird und wo Verbesserungspotenzial besteht. Indem Sie die OEE regelmäßig messen und analysieren, können Sie Schwachstellen identifizieren und gezielte Maßnahmen ergreifen, um die Effizienz Ihrer Produktion zu steigern. - Kosteneinsparungen:
Eine höhere OEE bedeutet in der Regel eine höhere Produktionsleistung bei gleichzeitiger Senkung der Produktionskosten. Durch die Identifizierung von Engpässen und die Beseitigung von Verschwendungen können Sie Ihre Produktionsprozesse optimieren und so Kosten einsparen. - Qualitätsverbesserung:
Die OEE bezieht auch die Qualität der produzierten Produkte ein. Durch die Steigerung der OEE können Sie also nicht nur die Produktionsmenge erhöhen, sondern auch die Qualität der Produkte verbessern. - Transparenz:
Die OEE bietet Ihnen eine klare und aussagekräftige Kennzahl, mit der Sie die Produktionsleistung Ihrer Anlage messen und vergleichen können. So haben Sie jederzeit einen Überblick über die Leistungsfähigkeit Ihrer Produktion und können schnell auf Abweichungen reagieren. Insgesamt kann die Verwendung der OEE dazu beitragen, Ihre Produktionsprozesse effizienter, kostengünstiger und qualitativ hochwertiger zu gestalten.
Ein Beispiel aus der Praxis
Problemstellung:
Bei einer Kurbelwellen-Bearbeitungs-Maschine betrug die mittlere Betriebsdauer zwischen Ausfällen bzw. Störungen (MTBF):
ca. 20 Minuten
Die eigentliche Reparaturzeit dauerte ca. 2 Minuten.
Jedoch bis die Störung bearbeitet wurde, dauerte es. Es vergingen oft 10-20 Minuten, bis ein Maschinenbediener an der Maschine war. Grund war zu wenig Personal.
Kalkulierte Ausfallkosten:
Kosten bei Ausfall der Maschine= 2.950 €/Std.
Bei längerem Stillstand fielen sukzessiv weitere Maschinen aus, bis nach ca. 60 Minuten die komplette Linie stand.
Ausfall der kompletten Linie:
82.600 €/Std. (28 Maschine a 2.950 €/Std.)
Lösung:
Durchgeführt wurde Wochenendeinsatz von Freitag bis Montag, wo Teile der Maschine gewartet und neu eingestellt wurden.
Die Reparatur hätte ca. 2 Arbeitstage in Anspruch genommen.
Zusätzlich haben Mitarbeiter des Kunden diesen Einsatz begleitet und wurden auf diese Maschinen geschult.
Neben den Reparatur- und Einstellarbeiten wurden weiteres Wissen vermittelt. Ziel war es die Zeiten für die Störungs-Analyse deutlich zu verkürzen.
Da die Instandhaltungs-Techniker durch die Zentralisierung ihrer Abteilung mehr als 20 verschiedene Maschinen-Typen betreuten, wurde hier wertvolles Wissen vermittelt.
Ergebnis:
Nach dem Einsatz erhöhte sich in mittlere Betriebsdauer zwischen Ausfällen (MTBF): auf über 24 Stunden
Der Kunde hatte so pro Tag zusätzliche 9 Produktionsstunden
Mehrwert 9 x 2.950 € = 26.550 € pro Tag